加工工程
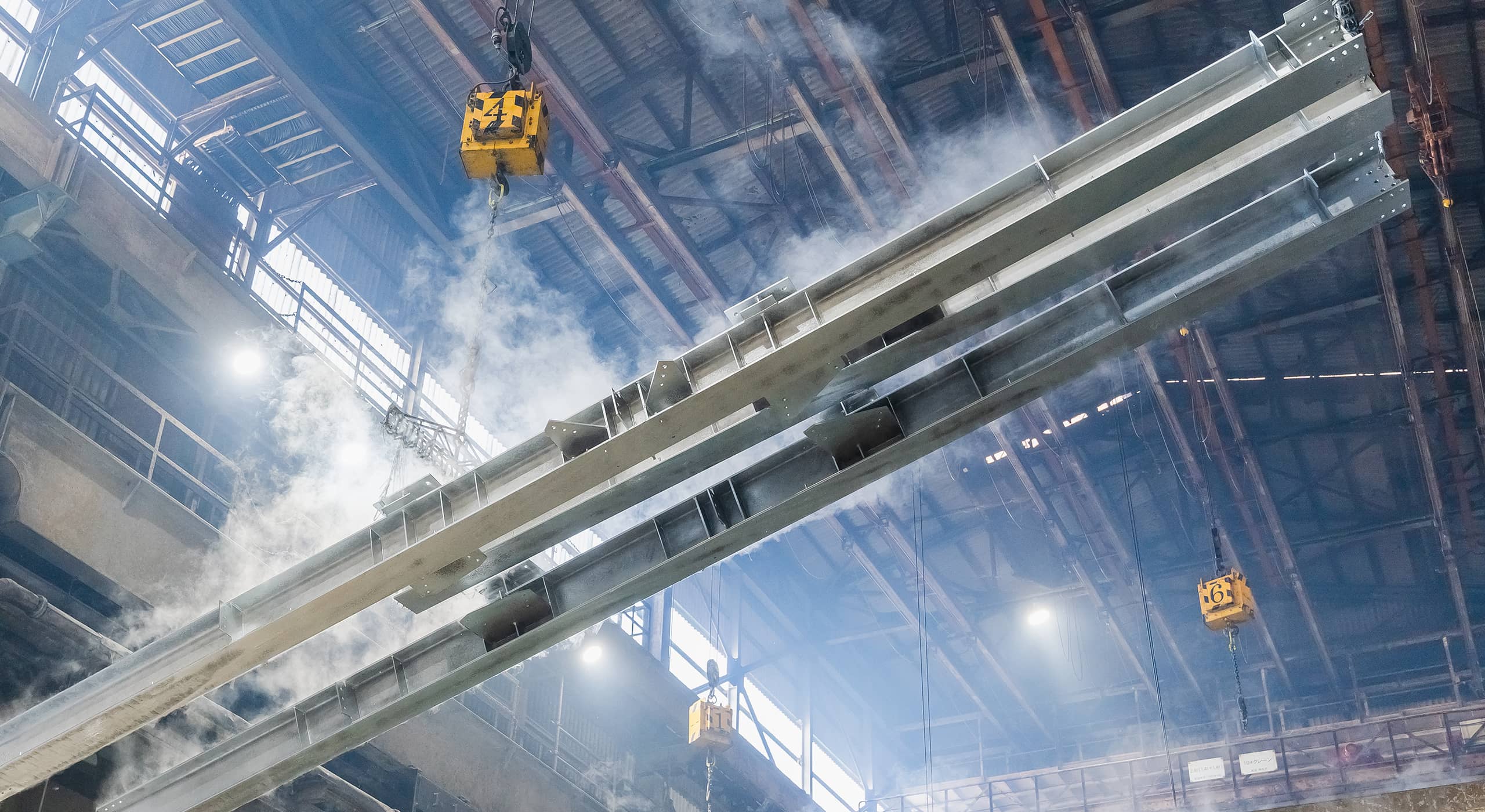
お客さまのニーズに合わせた高品質の製品を作るために、ひとつひとつのプロセスを大切に徹底した工程管理を行っております。
また、川崎工場は大中小3サイズのめっき槽を併せ持ち、お客さまのご要望に合うサイズのめっき槽を使用することにより、常に安定した品質を提供しております。
川崎工場 加工工程
素材受入
お客さまよりお預かりした製品の員数、形状、外観などを確認し製品を受け入れます。
受入検査
めっき適合の素材条件をチェック(予防処置)します。
前処理
脱脂
加温した5~12%の脱脂液に漬け込み、付着している油、ニスなどを除去します。
水洗
品物に付着した脱脂液を洗い流します。
酸洗
6~16%の塩酸に漬け込み、さび、スケールなどの酸化物を取り除きます。
水洗
品物に付着した塩酸と酸化物を洗い流します。
フラックス処理
塩化アンモニウム水溶液に漬け込み、酸化防止と鉄と亜鉛合金反応を促進させます。
めっき
溶融亜鉛めっき
440〜460℃に溶融した亜鉛浴に漬け込み、めっき皮膜を形成させます。
冷却
50~95℃の温水にめっき後の品物を入れ、合金反応の成長を抑制し、安定しためっき皮膜を形成させます。
歪み発生が予測される場合は空冷する場合もあります。
白さび防止
ご要望によりアクリル樹脂の浴槽に品物を漬け込みコーティングすることで、白さびを防止し表面を保護します。
後処理
仕上げ
めっき加工で発生するたれ、バリ及び付着酸化物などを除去し仕上げを行います。
検査
外観検査、付着量、密着性などのめっき皮膜試験を行います。
製品出荷
名古屋工場 加工工程
素管受入
お客さまよりお預かりした鋼管の員数、サイズ、寸法、外観などを確認し製品を受け入れます。
解束
受け入れた鋼管を解束し、次工程の準備をします。
前処理
脱脂
加温した脱脂液に漬け込み、付着している油、ニスなどを取り除きます。
水洗
品物に付着した脱脂液を洗い流します。
酸洗
加温した酸液に漬け込み、さび、スケールなどの酸化物を取り除きます。
水洗
品物に付着した酸液と酸化物を洗い流します。
フラックス処理
塩化アンモニウム水溶液に漬け込み、酸化防止と鉄と亜鉛合金反応を促進させます。
めっき
めっき
- 浸漬
- 引き上げ
- 外面ワイパー
- 内面ブロー
- 浸漬
- 自動浸漬装置により鋼管を亜鉛浴内へ浸漬させます。
- 引き上げ
- 自動引き上げ装置により鋼管を浴面より引き上げます。
- 外面ワイパー
- 鋼管の外面をワイピングにより、平滑に仕上げます。
- 内面ブロー
- 鋼管の内面を蒸気ブローにより、平滑に仕上げます。
冷却
- 空冷
- 水冷
- 空冷
- 曲がり防止のため空冷時間を設けます。
- 水冷
- 空冷後に水で冷却します。
後処理
検査
- 内外面検査
- 曲がり検査
内外面および曲がりを検査します。
矯正(曲がり管)
曲がり管を矯正機により矯正します。
塗油(白さび防止)
白さび発生防止のため防錆油を塗布します。
ネジ・内面加工
用途により管端ネジ切り加工および内面研削加工をします。
マーク表示
外面にステンシルマークを印字します。
結束
指定本数にてフープ結束します。
製品出荷